10+ years of experience
Always quick results
Advisory report always included
ISO 9001:2015 & VCA* certified
Perfect for detecting defects in magnetic material
Magnetic Testing offers quick determination of defects caused after welding magnetic material, thus avoiding high repair costs later on. NDO Nederland also always includes an advisory report is, allowing you to avoid similar future problems.
Magnetic Testing or Magnetic Particle Inspection (MPI) is relatively inexpensive, while you get quick results. We often conduct our tests on site as well.
- Applicable on all magnetisable materials
- Up to 6 millimetres deep
- Advisory report always included
- Short turnaround times
- Quick results
Satisfied clients
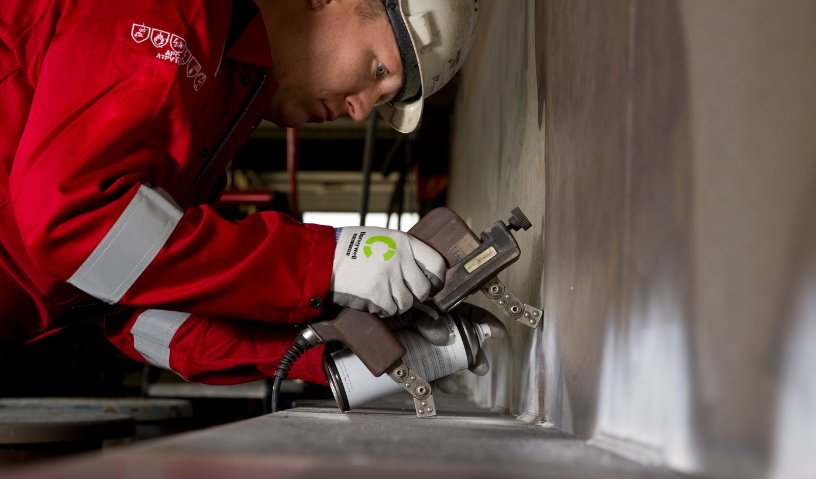
Need Magnetic Testing
ASSURED WELDING QUALITY OF MAGNETIC MATERIALAdvantages of Magnetic Testing
The main advantage of Magnetic Testing is it’s quick results as well as that it’s a relatively inexpensive. In addition, it is a typical form of Non-Destructive Testing, as it leaves practically no traces.
Depending on your wishes we use alternating current or direct current. Alternating current detects defects at the surface, while direct current can be used to detect defects up to 6 millimetres deep. The ultimately covered depth depends on the material we are testing.
Another advantage is that Magnetic Testing can be used for many different materials, provided they are magnetisable. This basically means all materials made of carbon steel, provided the coating is removed. In some cases a very thin layer of paint may remain on the surface.
Want a quick check to determine whether a joint welded in magnetisable material has any defects? Then Magnetic Testing the solution. It offers quick results and proves to be an easy way to exclude surface defects.
- Quick results
- Practically no traces
- Up to 6 millimetres deep
- Applicable on all magnetisable materials
- Relatively inexpensive
How does Magnetic Testing work?
Magnetic Testing is applicable on all magnetic materials at various moments. For instance after welding during construction, at grinding spots in the new development phase, but also during welding repairs. Thus you are ensured that the welding work does not have surface defects and also meets all requirements. Magnetic Testing can also be conducted at surface damages of parts or after maching such as turning and milling. Often Magnetic Testing is applied when a welding joint may have been over-stressed.
Relevant markets
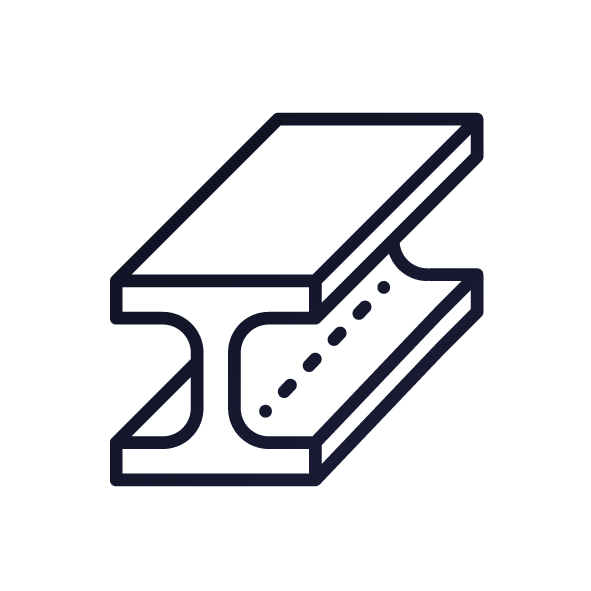
Steel & Non-Residential Construction
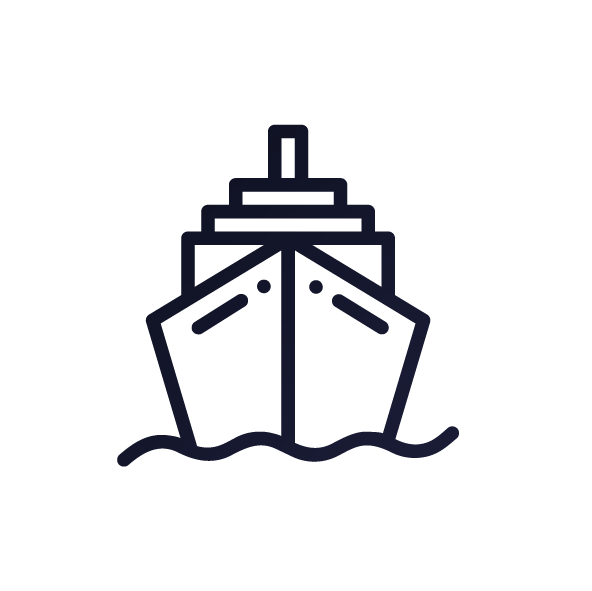
Ship Building and Repair
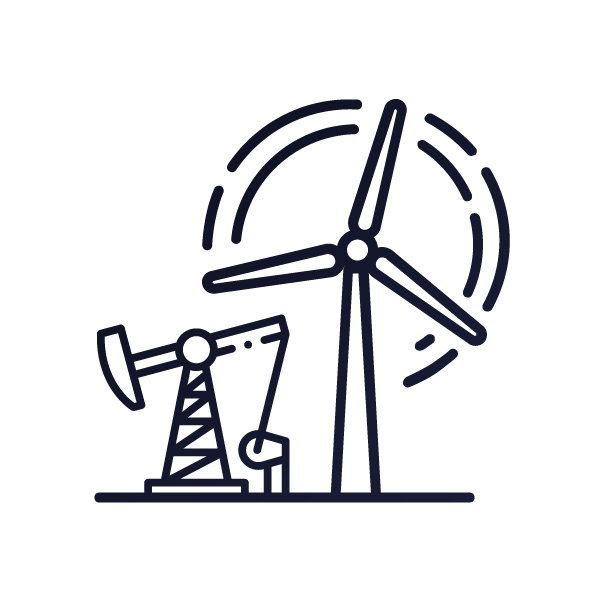
Oil, Gas & Wind
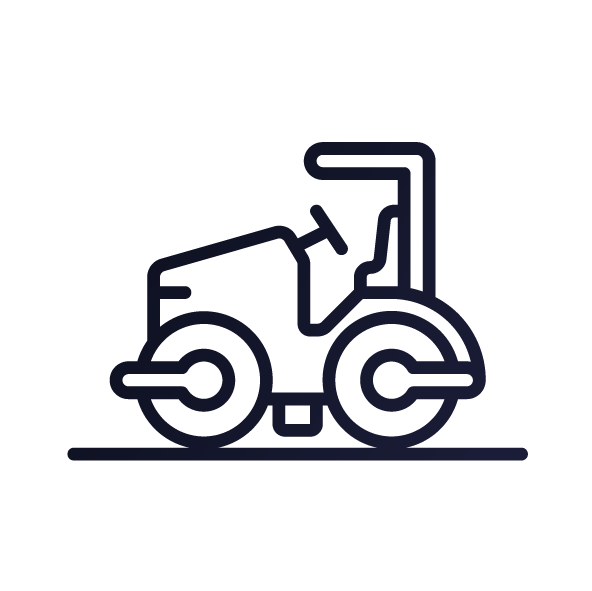
Civil Engineering
Frequently asked questions about Magnetic Testing
-
How does Magnetic Testing work?
In order to detect a defect, we use dry magnetic particles or a solution with oil or water in a contrasting colour. After magnetising the test object, we can precisely tell where a defect is. We can also use particles that re-emit UV light, allowing us to detect defects as small as 0.4 millimetres.
-
WHICH KIND OF METHODS DO YOU APPLY FOR MAGNETIC TESTING?
Magnetisch onderzoek wordt vooral uitgevoerd met wisselspanning. Op aanvraag voeren we het onderzoek ook uit met gelijkspanning. Dat doen we om dieper gelegen defecten op te sporen. Daarnaast kunnen we ook gebruik maken van olie of water in contrastkleur én uv-licht.
-
IS MAGNETIC TESTING POSSIBLE ON COATED MATERIALS?
The best results are realised with uncoated materials. In some cases the coating doesn’t have to be removed however.
-
IS SERIAL MAGNETIC TESTING ALSO AN OPTION?
It certainly is, we have specific magnetic tape at our disposal for this purpose.
-
CAN MAGNETIC TESTING ALSO BE CONDUCTED ON WARM SURFACES?
Yes, that’s possible. We have special products which allow this kind of testing.
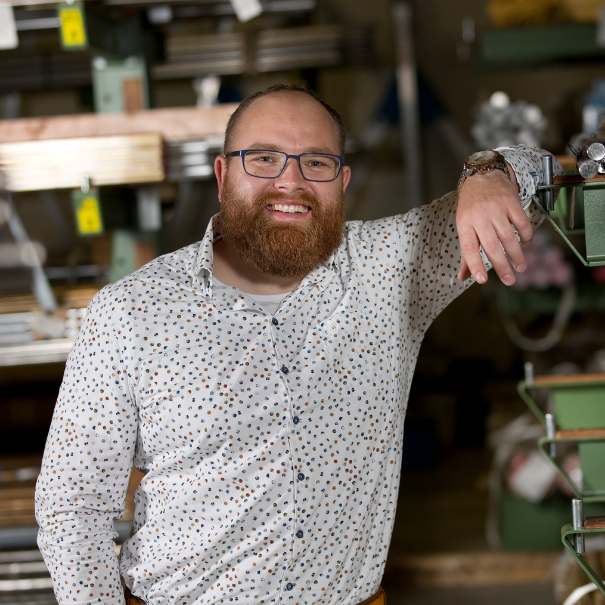
Request
a free offer
for magnetic testing
More interesting NDT methods
Reduce repair costs and avoid late delivery
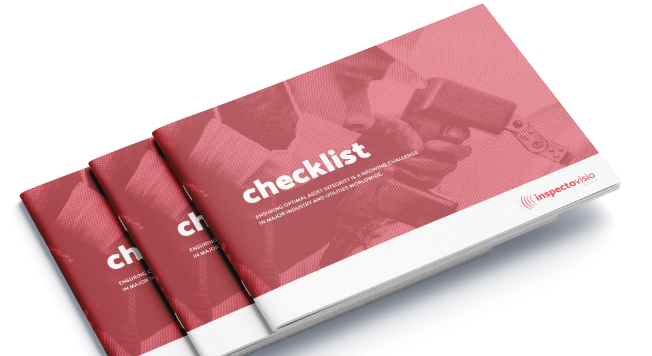